5S is a system for maintaining visual order, cleanliness and good organizational practices in the workplace. The acronym originates from five words in the Japanese langauge beginning with a letter “S”. Rough translations of these words, also begining with an S, can be found in almost any language, including English.
Definitions
1S - SORT
Physical separation of needed items from unnecessary and appropriate disposition of the unnecessary.

2S - SET IN ORDER
Visual labeling and exposing all needed items in such a way that everyone can find them and easily put them back in the right place.

3S - SHINE
Cleaning the workplace until it shines, while at the same time identifying wastes.
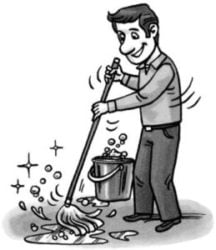
4S - STANDARDIZE
Establishing work standards that enable efficient use of the first three “S”.

5S - SUSTAIN
Maintain discipline in using the 5S, continuously raise the bar and improve the system using Visual Management.


Implementation Program
Implementation roadmap varies with company size and industry. Many successful sites follow this scenario:
- Create company structures supporting the implementation process: Champion, Steering Committee and internal trainers.
- Divide the site into zones and develop an implementation roadmap adjusted to available resources. The whole implementation should take no more than 2 years.
- Conduct initial training in the zones and implement according to roadmap.
- Develop and implement a control system such as daily patrols, monthly audits, etc.
- Develop and implement a Visual Management system with metrics showing critical process parameters as well as 5S levels.
The above scheme illustrates “hard” elements of change implementation. Successful companies put just as much emphasis on the soft elements: motivating employees, promoting successes and training managers to become true leaders of the workplace.
Train-the-Trainer
Enables conducting 5S workshops using internal resources and implementing the system autonomously. More information.
5S Benefits
5S Workshop
The workshop combines learning foundations of 5S with their implementation in the pilot area. Participants identify and remove unnecessary items, clean and organize the area in a visual manner. They also brainstorm work standards that will help sustain generated improvements.
The workshop is illustrated with examples from various industries. At the end the team presents results to management.
Participants: max. 12 people
Duration: 2 days x 8 hours
DAY 1
- Introduce foundations of continuous improvement, link to Lean Management
- Conduct 5S Simulation
- Explain and implement 1S – removal of unnecessary items
- Cover 2S – role of visualization in workplace management
- Teach 3S – inspection while cleaning
- Develop a plan to implement 2S and 3S
DAY 2
- Implement action items in the pilot area
- Develop work standards – 4S
- Conduct 5S audit
- Present results to management
Literature
5S Book – in the Polish language